一、參評企業基本情況
美的是一家消費電器、暖通空調、機器人與自動化系統、智能供應鏈(物流)的科技集團,在2017《財富》世界500強排名中位列450位,利潤排名第208位,并擁有約13萬名員工。作為中國家電行業龍頭,美的一直堅守“為客戶創造價值”的原則,致力為人類創造美好生活。在新時代的契機下,美的不斷向國際化、多元化方向發展,2016年收購德國機器人制造商庫卡意味著美的進入了自動化生產與人工智能行業,美的從傳統制造業向國際化科技制造行業的轉變,體現了美的人不斷求創新、謀發展的精神,相信在未來的道路上美的將會引領中國制造業走向國際,不斷取得新的輝煌。

圖1 美的集團總部
二、企業在智能制造方面的現狀
美的集團作為一家領先的消費電器、暖通空調、機器人及工業自動化系統的科技企業集團,不斷深化轉型,勇于改變,緊抓機遇,追求新的增長,踐行“一個美的、一個體系、一個標準”,圍繞業務戰略、互聯網戰略、全球化戰略三條戰略主線,由單一產品的制造商轉向提供系統集成服務方案商,實現商業模式創新。截止2017年《財富》世界500強第450位,營業收入2200億,資產總額超過4000億。
回顧美的集團智能制造發展歷程,總體可分為三個階段。
起步發展階段。自2008年開始,為滿足單一的外銷產產品品質追溯應用的業務訴求,美的開展了傳統MES的建設,對生產結果記錄,并記錄關鍵件品質的信息化建設,提高了某些業務領域的工作效率,代表著智能制造信息化的起步。
2013年起,隨著智能制造信息技術的快速發展,美的集團結合現狀,為滿足精益管理對制造信息化的迫切需要,自主開發了相關業務智能制造業務應用,進入了全面制造信息化應用的階段。形成了垂直式的集團式MES管理平臺,打造了智能制造標桿,橫向集成、縱向貫通,在全流程品質,計劃斜接及執行,物流拉動,數字化透明工廠及移動化,設備聯機等方面不斷取得新的進展、新突破。美的集團進入了以“智能制造+智能產品”雙智戰略為標志的新時期,智能制造發展進入了以構建科學、精益、高效管控的新階段。
三、參評智能制造項目詳細情況介紹
1.項目背景介紹
美的集團在2012年確定了632戰略,歷經三年完成全集團九大事業部實施和推廣,全面重構美的信息系統,形成了6大運營系統、3大管理平臺、2大門戶和集成技術平臺。踐行一個美的、一個體系、一個標準,統一端對端流程和主數據,通過信息化手段對價值鏈進行全流程管控,數據流清晰透明,為未來進一步數字化轉型打下了堅實的基礎。在此背景下,結合集團“雙智戰略”,順應制造行業的轉型趨勢,原MES平臺已經無法滿足智能制造的需要。
原MES平臺由多套子平臺各自發展,產品技術平臺多樣、實施商水平差異大導致產品規劃不足,主要針對業務痛點局部滿足業務操作需要居多,同一套平臺功能差異化多,以數據對象實現全部的業務邏輯,可擴展性差,耦合度高。在應用架構上沒有模塊化和標準化,很難實現功能和規模的擴展重點側重實現現場操作層需求,因現場布局、管理要求、操作習慣、工藝流程、設備等差異以及多個實施商實施,造成同一功能存在多個版本支持不同基地使用。由于分散建設,功能標準化、通用性不足,導致推廣實施成本高。因此,如何打造一個集團層面的數字化精益MES平臺,實現訂單跟蹤全程追溯,與供應商互聯,過程自動智能化,品質在線管控,數據采集及大數據應用,聚焦交付精準、效率提升、品質改善、數字化透明是一個迫切需要解決的課題。
2.項目目標與實施原則
本項目引入數字化車間技術與智能制造模式,提升制造全價值鏈優勢,項目以實現自動化及設備聯機、生產透明化、物流全流程管理、管理移動化、決策數據化為目標。采用自動化產線CPS物理信息網絡,突破數字化車間智能感知技術與裝置、數字化車間生產執行管控,涵蓋入場材料物流、場內成品管理、生產執行、物流配送、制程品質,實現總裝及部裝零部件加工的全過程數字化制造與精細化管控,縮短產品制造與交付周期,提升制造信息化精益水平。
3.項目實施與應用情況詳細介紹
3.1 項目架構
3.1.1 總體架構
一個核心,六個維度:以智能精益工廠為核心、結合智能自動化、智能機器人、智能物流、智能信息化、移動大數據、物聯網集成等六大關鍵技術應用,實現美的智能制造
3.1.2 業務架構
業務架構是用來將其后架構工作的業務價值闡述給相關干系人所必不可少的,在業務架構過程中,將盡量重用各種已經存在的成熟的材料,并且針對信息的收集和分析也應該依據架構工作的范圍而采用那些能夠促成明智決策的信息。在本項目方案的業務架構過程中,延續632管理精神,由業務主導,采用業務Sponsor負責機制。項目規劃、設計、研發、實施、測試等工作的各類人員進行統一全程管理。同時,對項目開展全過程規范化管與建設實施質量評價,開展項目PMO管理機制,采用日報、周報、月報等形式及時掌控、部署階段工作任務。周密計劃、剛性執行,嚴格把控各個里程碑節點。
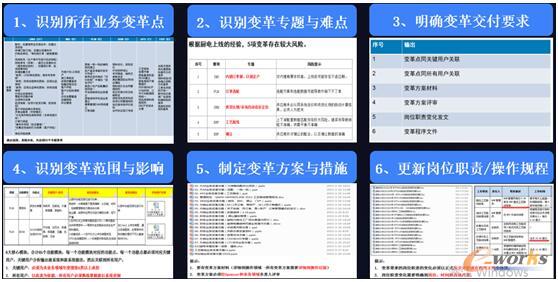
圖2 項目的業務架構
3.1.3 應用架構
根據業務流程以及各流程之間的關系,確定了美的產品化MES平臺的業務應用框架藍圖。以實現物流拉動、過程管控、品質管控、自動化生產、工廠可視的業務價值。MES平臺形成十大業務應用功能模塊,并實現模塊間緊密集成,達到支撐業務高效運作的目標。
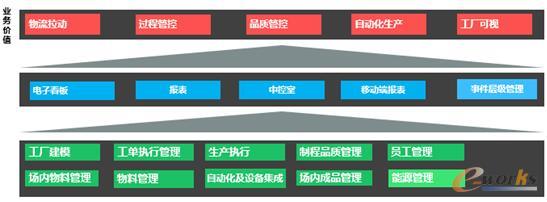
圖3 項目的應用架構
3.1.4 技術架構
依據美的集團目前的業務管理模式,業務處理復雜程度、數據量大等因素,采用分布式部署的模式,按照企業級信息系統的理念進行設計和開發,業務應用基于一體化平臺構建,在集團總部和各省基地兩級進行部署,業務應用和保障體系組成完整的信息系統。
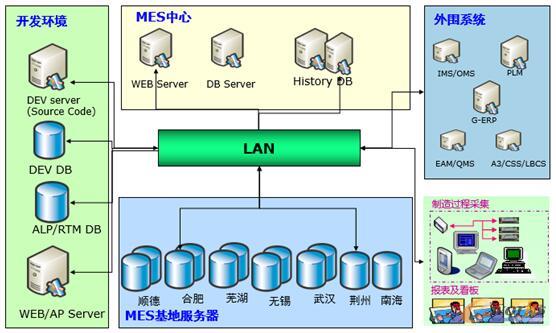
圖4 項目的技術架構
3.2 精益數字化MES平臺典型應用
3.2.1 過程品質管理應用
實現制程品質防錯防呆、制程質量自動預警,以及制程數字化、智能化、可視化的管理目標。內容包括制程基礎數據管理、制程數據采集(物料數據采集、設備數據聯機、質量缺陷采集、人員崗位數據采集、兩圖一書)、制程控制防呆錯、制程數據分析、制程質量追溯、制程改善閉環等六大PQC產品化功能的方案規劃、設計、開發與上線試點,形成了一套完整的閉環管理的數字化驅動的制程控制管理體系。
●從人、機、料、法多方面結合系統在制程方面實現防呆、防錯,包括關鍵崗位人員的管理,關鍵設備點檢和檢定周期管理,測試設備聯機取值及結果判定,物料可用性、合規性、生產過程中的工序防錯、不良品管制及不良品的自動分流排出、返修定責再次上線。

圖5 在制程方面實現防呆、防錯
●關鍵件采集:在投料時,檢查物料的檢驗狀態,不合格品或者未檢驗的物料無法投料使用;檢查所裝配物料與工單BOM一致性比對,不符合工單BOM需求的物料無法被裝配使用。
●兩圖一書:QC工程圖、工藝流程圖與作業指導書。
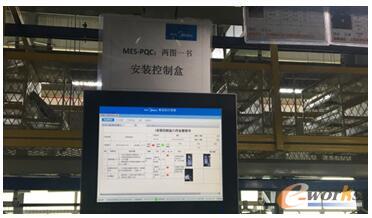
圖6 兩圖一書管控
●質量缺陷數據采集及控制:控制各生產線產品的實時狀況及缺陷分布比例,如良品率等,在品質趨于異常或發生異常時自動推送通知或控制停線整改。
●SPC分析:耐壓/絕緣測試、泄露測試、四合一安規測試、功率測試實現設備聯機,每條生產線配置一個線服務器、四個檢測崗位、數據采集器、固定掃描器、觸摸屏PC,觸摸屏終端放置在四個檢驗工序,檢驗人員通過MES客戶端進行不良數據錄入,連接設備工序測試結果(如NG)直接輸出工序客戶端自動錄入,數據通過網絡傳輸到服務器,并根據定義SPC規則推送相關品質信息。

圖7 SPC分析
3.2.2 基于拉式生產的“無紙化”物流管理應用
物流管理作為供應鏈物價值鏈中的重要一環,我們基于價值流理念與實際工廠管控結合,實現供方物流按時刻入場管理,追蹤物流信息提高供方入場的物流效率。拉通場內各物流管理場景,通過不同維度的追溯管理機制,實現MES的庫存管理。進一步提高場內物流的數據實時性和準確性。
●實現與供應商端拉通,強化入場物流路徑強控,實現與供方信息互聯:通過與供應商的協同管理,對過程的確認送貨、備料、發貨、裝車、運輸、軌跡、入場、卸貨、出廠等狀態進行精準定位控制管理。

圖8 實現與供應商端拉通
●物料齊套管理前移,提升并保障客戶交期預判精準度:采購管理的信息采集與溝通方式發生質的變化,采購員對過程的物流信息得到全方位的控制管理,實時分析檢索工單配套物料的整體配套信息及狀態。
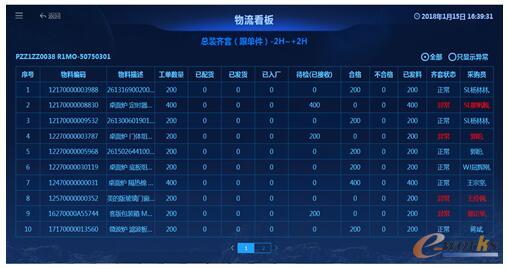
圖9 物流看板實現物料齊套管理
●運輸成本透明輔助供方使生產園區進出卸貨井井有條。
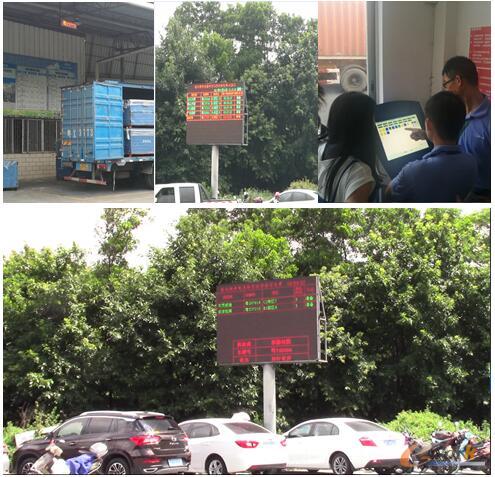
圖10 園區卸貨的管理
●物流協同實現無紙化管理:供方物流全面取消送貨單打印及過程手工簽核管理,通過手機APP進行車位預約,全流程通過車牌+條碼按車次對過程物流狀態進行物料移動追溯管理,全流程支持多平臺實時檢索查詢,過程物料的簽收實現按車次批量接收處理。供方按車次做到按批次核單對數,核銷周期由天轉變為按車次控制,每月節省20萬張以上的送貨單據。
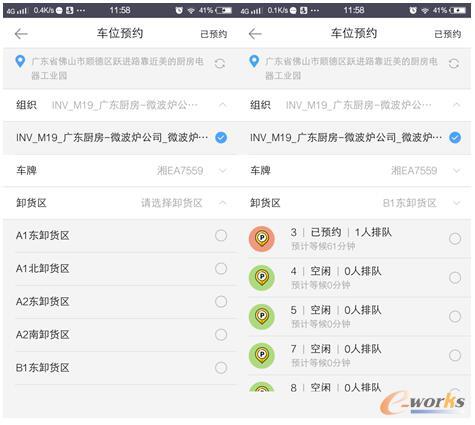
●場內總部裝拉動及賬務實時拉通:實現入場物流、自制件物流、場內物流的財務拉通管理,通過工序及完工實現拉動配送發料管理及同步賬務處理。對現場貨區貨位實時自動推薦管理。
3.2.3 精益化車間安燈管理
提升制造車間現場日常管理水平,實現了問題閉環管理、關鍵KPI優化提升、會議及點檢等流程固化、責任清晰及有效響應。
●目視化關鍵指標:不同層級(線體-區-分廠)的會議展示不同維度(班組-日-月-年)的關鍵KPI,所有該關注的問題一覽無遺,同時展示一段時期以來的趨勢,增加對改善目標如UPPH、不良率、安燈、點檢的敏感度,及時優化。
●目視化管理,通過ANDON提升事件的SLA和OLA水平,當前責任人響應、處理超時逐級通知上級領導,直到總經理。
●固化點檢流程、移動化作業并進行目視化:規定點檢清單及責任人,定時提醒點檢并記錄超時,同時提供移動化強化點檢日常管理。在每日會議看板中清晰可見,督促點檢及時發現問題。
●矩陣式分配責任及跟蹤:從不同的部門組織,抽取同一職責的同事設定為同一處理組,共同承擔責任,實現矩陣式管理,強化協同工作。多種系統終端,提升管理效率:除了提供傳統的美信通知外,還提供手表通知點檢、安燈等,并可通過PC、手表響應,使用平板點檢等,提高日常管理的效率,促進發現問題,解決問題,提高閉環率。
3.2.4 總控中心及移動化
以3D建模的形式展現工廠/車間/產線/設備等總體狀態,關鍵數據在模型中展示,多系統的數據集成,成立總控BI平臺,并展示核心BI數據;日、周、月、年度相關的Q/C/D數據進行趨勢分析,相關交叉分析,無序交叉分析,并進行智能預警提示。
●產量類看板
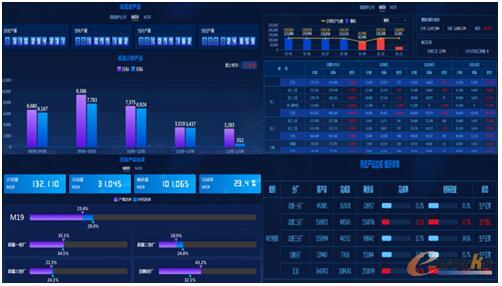
圖12 產量類看板
●品質類看板
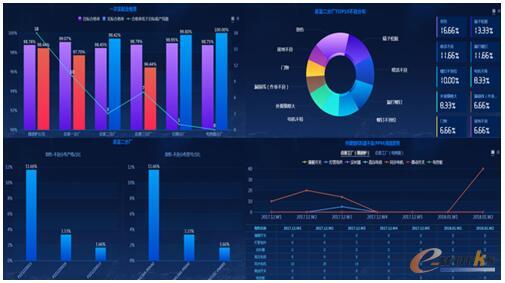
圖13 品質類看板
●物流類看板
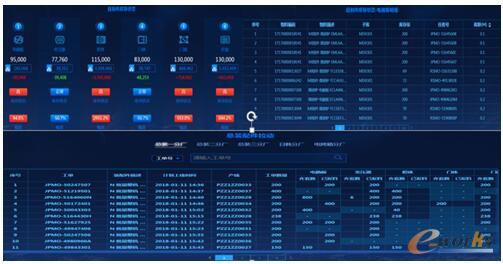
圖14 物流類看板
●3D建模的數據分析
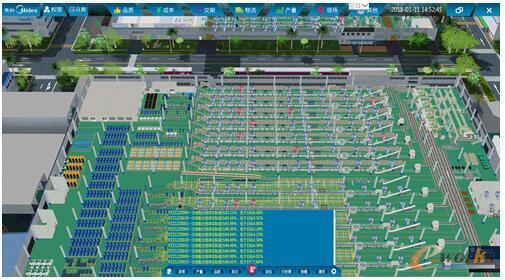
圖15 3D建模的數據分析
●移動化智造+
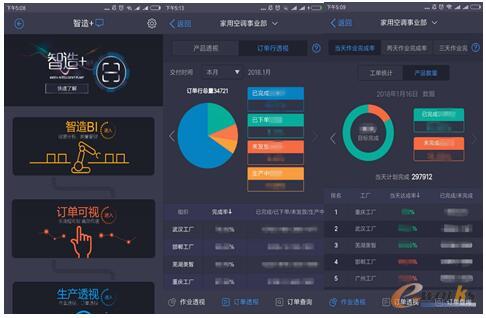
4.效益分析
4.1 數字化精益MES建設和應用主要成果
通過近年來的制造信息化建設和持續推動數字化精益MES平臺的建設,美的集團實現了總部、事業部、基地工廠的三層應用,建成了一體化的企業級的MES系統,已全面覆蓋全集團34家工廠,1000+產線,取得了顯著成果,極大的促進了制造信息化效能。在制造領域,實現了制造端縱向貫通、橫向集成,價值鏈拉通,信心化能力顯著提升,支持集團化運作。計劃源頭中已搭建三層計劃體系,S&OP產銷協作,提高物料通用性,融匯價值流的拉式為主,推拉結合的計劃模式,訂單拉通T+3模式,預排、產能可視,提高接單效率,縮短供貨周期。場內、外物流基于計劃穩定的價值流拉動,達到供方庫存透明,IQC品質檢驗標注化與剛性執行。計劃、來料、生產消耗環節信息透明與拉通。在生產過程品質,重點關注品質的時控及操作防錯,MES驅動揀料及配送防錯,PQC結合設備聯機SPC分析,通過預警、中控室實現過程品質控制。通過物料標簽與MO票結合,實現端對端的追溯,不僅僅追溯物料,而且追溯制造工藝參數。持續優化業務流程,壓縮業務層級、洞察業務痛點,實現精益化管理。
目前美的MES平臺日應用人數近10萬人,每天通過系統產生60萬財務交易憑證上傳,100萬物資出入庫記錄,管控90000多個生產作業過程,覆蓋制造全流程的采集與追溯,基于MES的數據歸檔每日30G。實現了制造過程中人財物等重要資源的集約化管理,連接自動化機臺和產線,自動化物流,入場、總部裝物流拉動,看板移動,訂單跟蹤,數據分析與展現等決策數據化。以上,獲得省部級以上的獎勵和表彰10多項,其中多個基地項目被國家有關部委評為國家信息化試點和示范工程。
4.2 制造信息化效能、效率和效益顯著提升
MES平臺有效固化了業務流程和管理標準,支撐了精益管理的集團化和扁平化。通過全流程可視化和數字促進任務流動,在632系統的基礎上(6大營運系統、3大管理平臺、2大門戶和集成技術平臺),向大供應鏈體系延伸,加速各環節任務流動。通過拉式生產系統實現JIT,根據物料屬性及消耗觸發配送指令、配送管理、信息展示,實時刷新任務上線時間、生產進度、損耗、交貨期數據的展示,提升制造綜合效率33%,降低原材料、在制品庫存90%。通過系統“防呆、防錯、防漏”,檢查數據自動采集,SPC預警等實現了“出現異常設備會自動停下來的‘自動化’的精髓”,減少生產損耗68%,改善產品品質10%。通過大數據應用,堅持PDCA改善,不斷提升目標值,將量化數據轉化為行動力,實現了生產管理的專業化和標準化,推動管理分析從統計型向分析型轉變。精益化MES已經深入到制造管理的各個方面、各個環節,通過信息流拉動和貫通共享,提升業務管控能力,為管理創新創造了新的局面。